Have you seen how pipes are delivered during construction? A large truck carries a dozen, sometimes three or five, pipes. They are usually transported from factories and warehouses a long way away, and the cargo is mostly air. Only 10% of the cargo represents pipes.
Next, the completed products are offloaded at the construction site and stored in a warehouse, and only afterwards they are laid and welded.
This process remained unchanged for over half a century until the Ukrainian company Pipes.One decided to challenge the inefficiencies of the classic scheme and created the world’s first polymer pipe factory on wheels. It is a mobile unit that arrives directly at the construction site and produces pipes with the required diameter and length on the spot.
Can you imagine a massive printer on wheels for producing pipes? One that prints the required length of pipe in one piece, even if it is 50 or 60 metres? A printer that operates next to the trench so that no crane is needed. In simple terms, this is what Pipes.One has developed.
To enter the Ukrainian and EU markets with such innovations, the company first had to obtain certificates of conformity. They did this with a grant from the Climate Innovation Vouchers program, funded by the EBRD with support from the EU and implemented in Ukraine by the NGO Greencubator.
In this article, Serhiy Sereda, co-founder of Pipes.One, shared his insights on the uniqueness of the development, the specifics of the polymer pipe industry, and the company’s progress.
The story of Pipes.one is a part of the series "The Cream of the Crop of Ukrainian Cleantech". It features 10 cleantech champions who received Climate Innovation Vouchers at a critical stage of their development. Climate Innovation Vouchers is one of the largest grant programs in Ukraine for innovators in green and climate-friendly technologies. It was initiated by the European Bank for Reconstruction and Development and funded by the European Union. Greencubator implements the program in Ukraine.
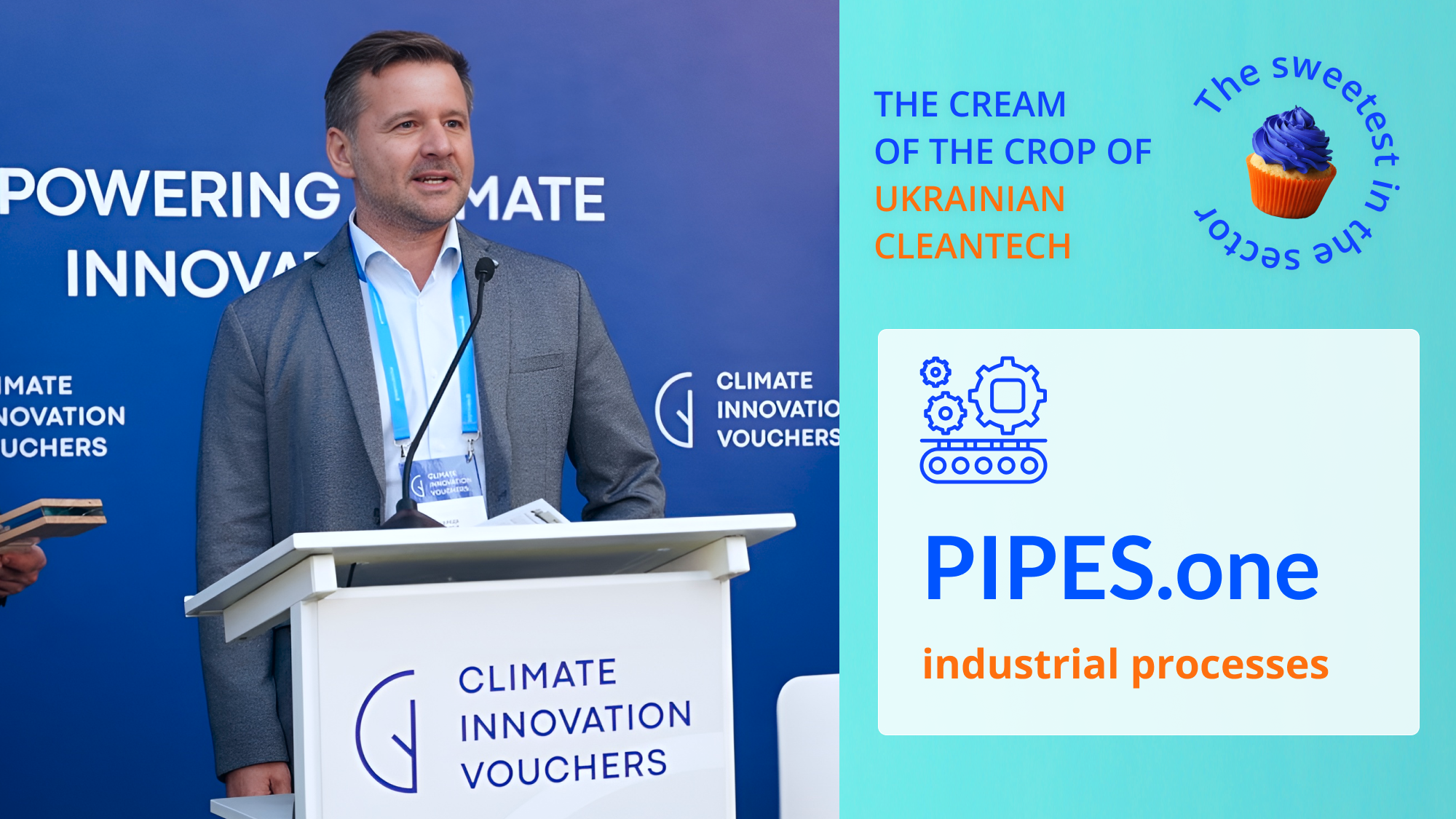
How does it work?
“We are a team that strives to bring innovations to the construction industry and simultaneously reduce the negative impact on the environment,” — says Pipes.One.
With over 25 years of experience in the construction industry, the company’s team saw how time-consuming, expensive and sometimes environmentally unfriendly pipelines can be. That’s how the team came up with the idea. Instead of transporting ready-made pipes by truck, the team decided to make them directly at the construction site. The company brought this concept to life by creating an industry-leading “pipe factory on wheels”.
A mobile plant is a unique unit placed in a truck trailer. It arrives at the construction site and produces the pipeline in the exact diameter required for the project. Just imagine: such equipment usually demands about 1000 sq m of production space.
In practice, the process looks like this: the mobile unit is connected to a bay with raw materials in the form of a plastic profile tube. The system welds the plastic and forms a pipeline tube that meets the required diameter and parameters.
A standard 3D printer can produce plastic moulds of any shape, but no larger than its work surface. Pipes.One technology, on the other hand, allows the production of round pipes with a length exceeding the unit’s size by dozens or hundreds of times. The engineers simply set the necessary diameter and length of the pipeline and “print” it.
“Thanks to this method, we can produce a pipeline of any length — 200, 300 metres or even a kilometre – without joining. Moreover, in our mobile unit, we can print pipes with diameters varying from 60 cm to 2 metres!” — explains Serhiy Sereda, co-founder of Pipes.One.
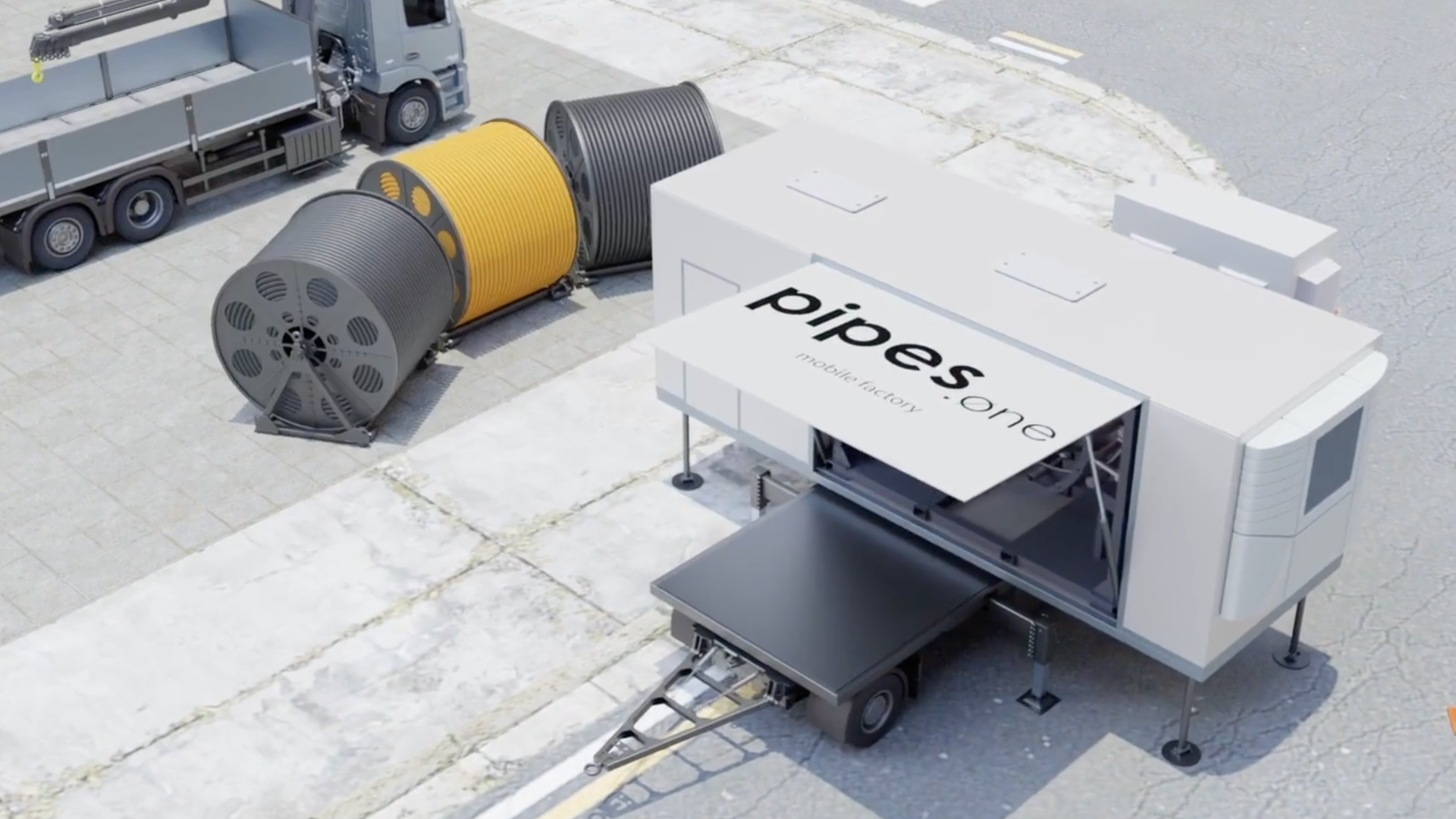
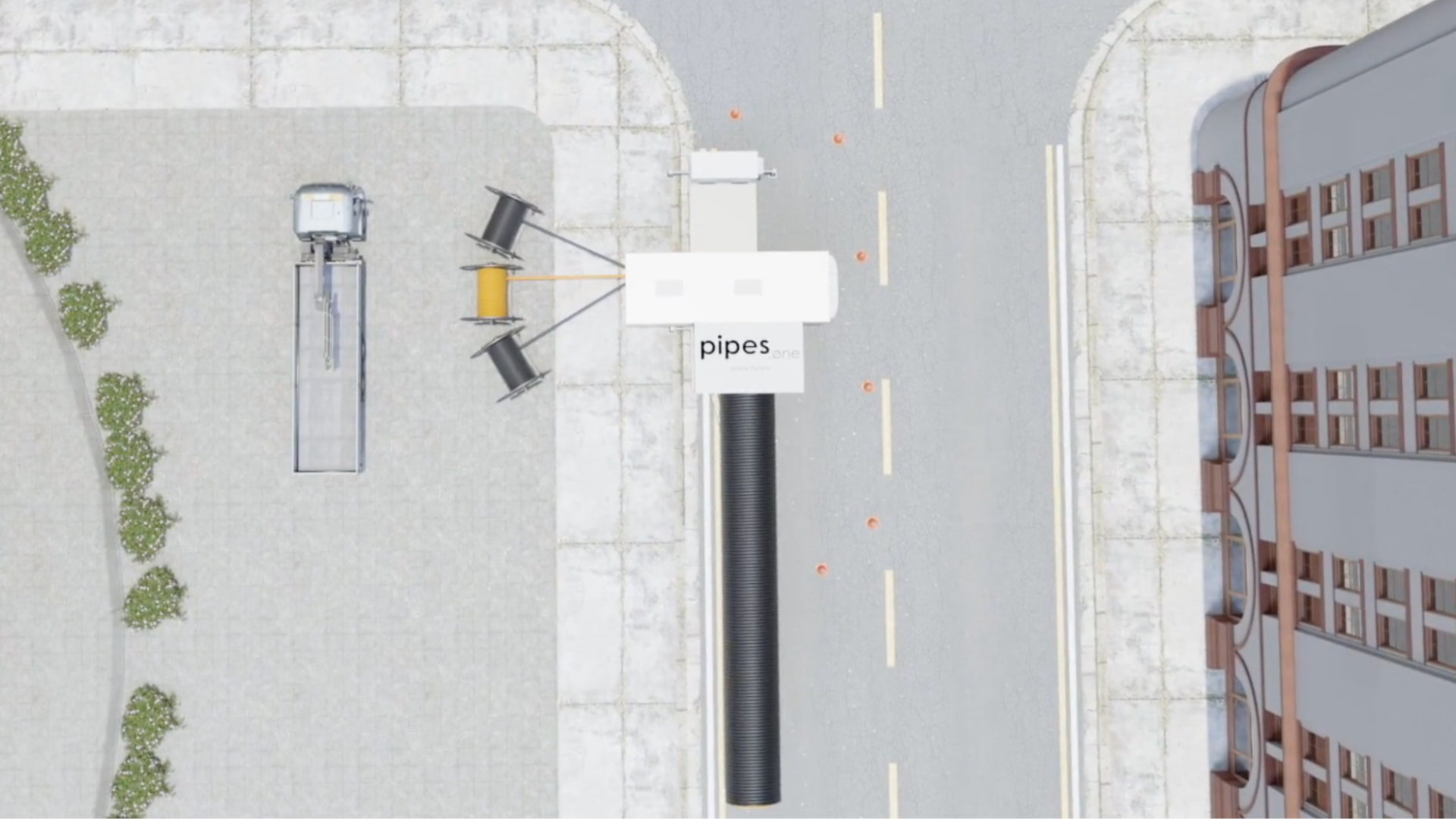
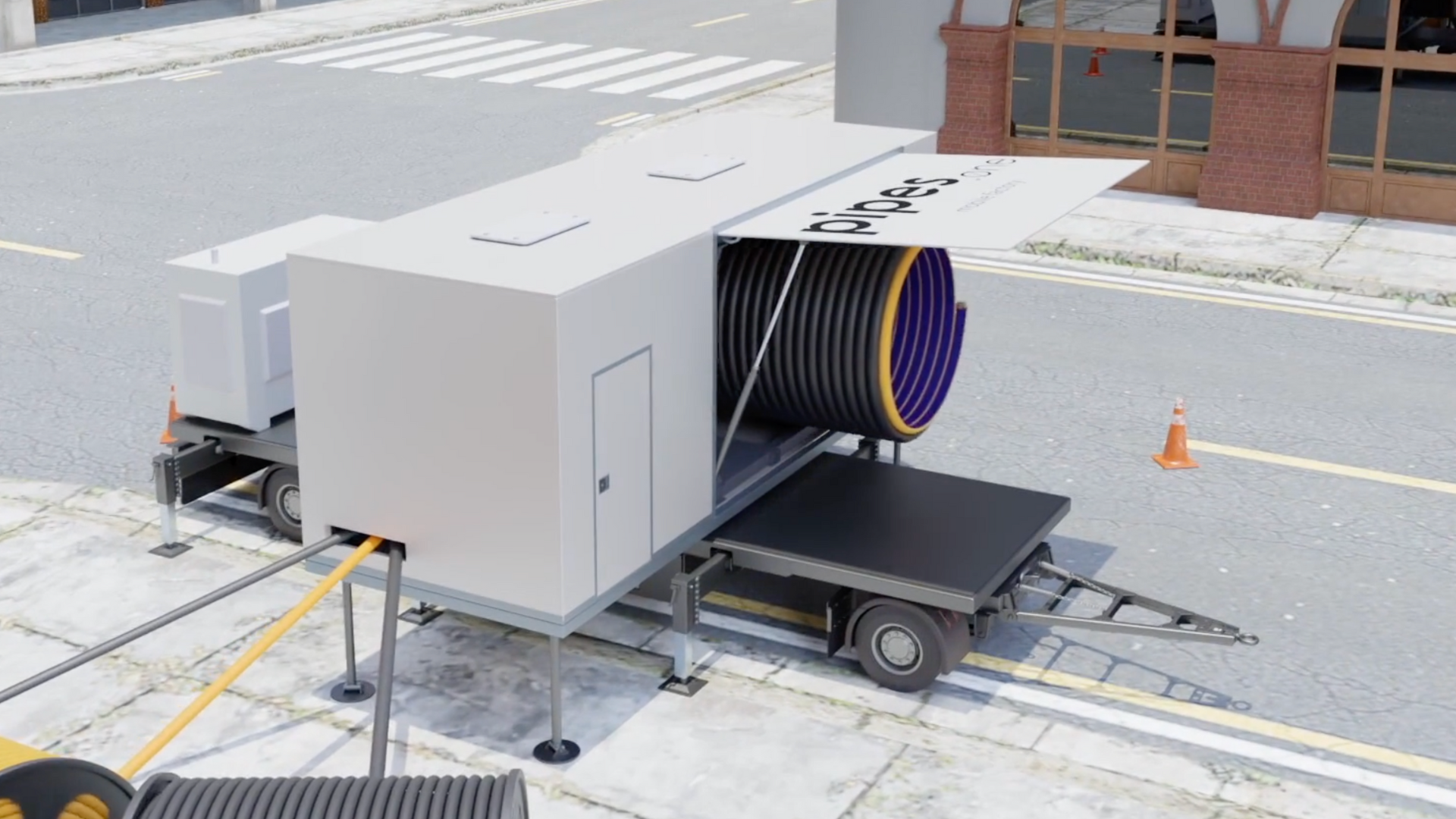
Such pipelines can be used for various purposes: sewage, drainage or agricultural irrigation. In addition to speeding up manufacturing, Pipes.One also reduces production costs. For instance, businesses can save money on logistics, joining pipeline elements, and storing ready-made pipes. Furthermore, their environmental footprint decreases. How exactly?
Firstly, the cost of shipping manufactured pipes can be cut up to 10 times, leading to a direct drop-in CO2 emissions from trucking.
Secondly, the raw material for pipes is polymer pellets made mainly from oil. Such synthetic polymers have a high carbon footprint, meaning that during their production, large amounts of carbon dioxide are released into the atmosphere. This leads to global warming and climate change. Pipes.One offers a more environmentally friendly solution.
“We have invented a range of innovations for our mobile production. For example, for a certain type of pipe, we have reduced the need for raw materials up to 34%, and thanks to the internal protective layer, we can make pipes by adding a specific amount of recycled material, making the process more sustainable,” — says Serhiy Sereda.
From idea to market launch
It takes work to revolutionise the polymer pipeline market. This industry is highly conservative: the last innovations occurred 50 years ago, and the entry threshold for new companies is extremely high. This means that to launch a new technology, you have to run many tests, get certification and prepare the necessary technical documents. These were the challenges that Pipes.One faced.
“We produced goods and tested the market. However, it turned out that even with cutting-edge innovation, it is challenging even to start a conversation with distributors and potential clients without certification. To enter the market, we urgently needed certificates of conformity, although they are quite expensive and time-consuming. That’s why we were seeking additional funding,” — recalls Serhiy Sereda.
To obtain the necessary documents for entering the market, the company received a grant from the Climate Innovation Vouchers. This grant program is funded by the European Bank for Reconstruction and Development with the support of the EU and is managed by the NGO Greencubator in Ukraine.
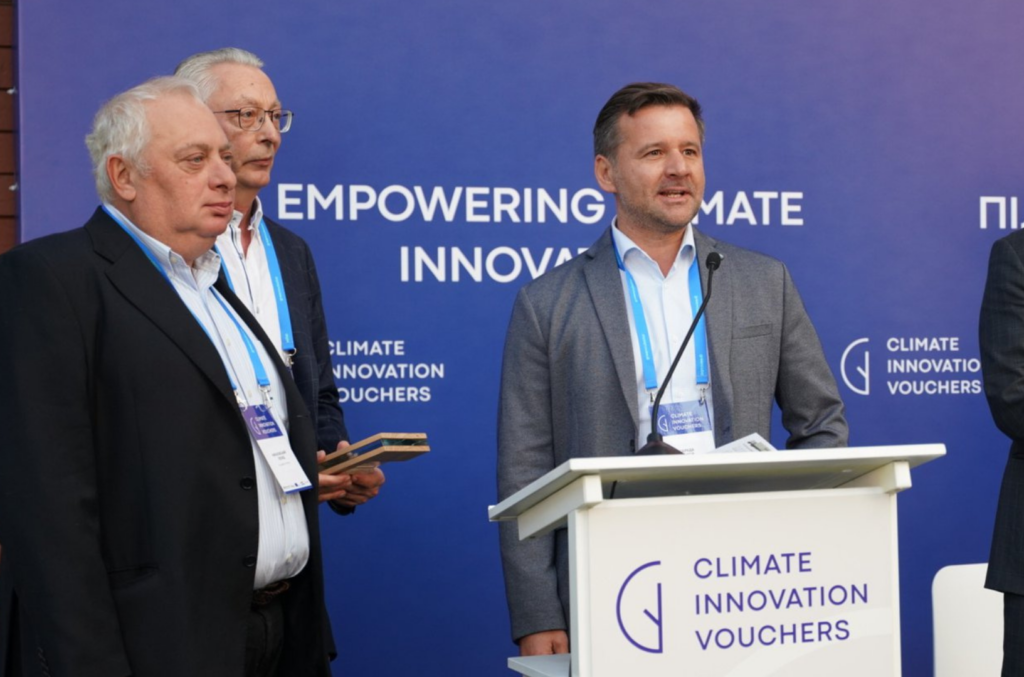
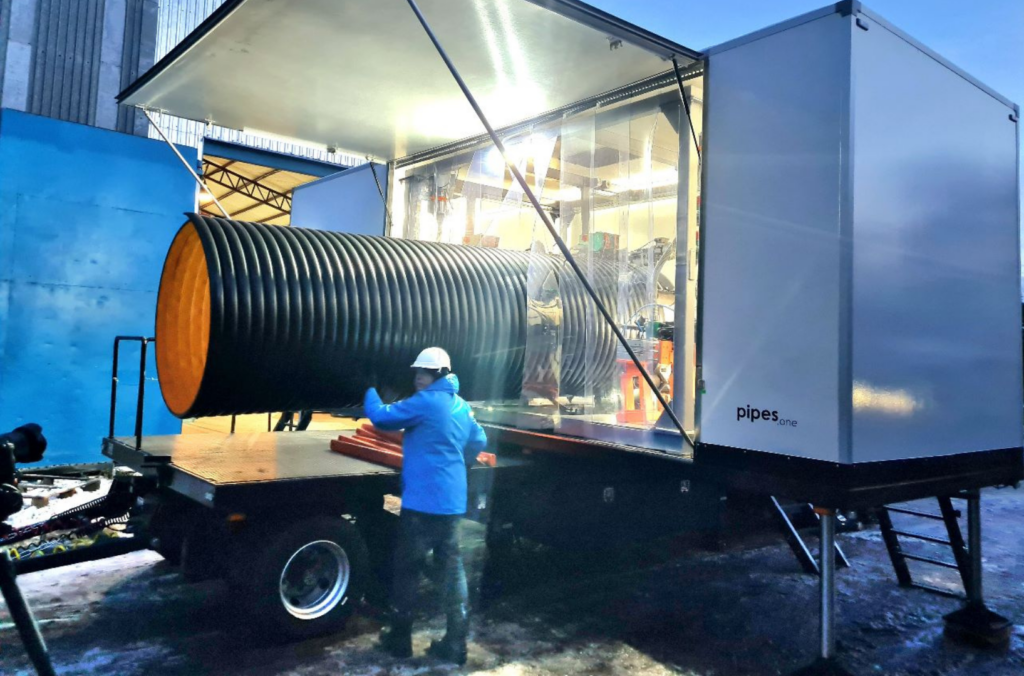
With funding from the Climate Innovation Vouchers program, Pipes.One has completed all the necessary technical documentation, obtained certificates for their technology in Ukraine and the EU, and ran the required tests.
To bring its product to the market, the company also had to patent its invention. Serhiy Sereda explains:
“Considering that our solution is based on a unique invention, we had to patent it. Only a patent allows us to protect an important market from potential competitors for 25 years. So, we identified key markets and applied for patenting. Overall, the process was expensive and took nearly three years; however, we went through it. Today, you have already obtained patents from the European Union and the United States.”
Ambitious projects and the recovery of Ukraine
In 2024, Pipes One actively grows. The company has successfully completed a grant program from Horizon Europe of about €1.8 million. The European Innovation Council (EIC) decided to continue cooperation and act as a co-investor in the company’s development. Serhiy Sereda was also appointed EIC ambassador in Ukraine.
Pipes.One has already implemented its first pilot projects across Ukrainian cities and received recognition for partnership from local authorities. The team intends to work on larger-scale cooperation. For instance, the company is negotiating with local partners in the EU, the US, and the Middle East to launch licensed production.
The current portfolio also includes completely unusual and groundbreaking projects. As an example, Pipes.One is working on an underground delivery solution in London. A British company has developed a way to deliver goods using electric trolleys via pipelines. A customer will make an order, which will be collected at a warehouse outside the city and delivered to the pickup point via underground tunnels. According to initial estimates, this development can remove up to 40,000 trucks weekly from London’s roads.
Also in 2023, the Pipes.One team used its technology to protect Ukrainians from Russian shelling. They developed a waterproof, heat-resistant, modular underground shelter based on polymer structures. This shelter can be used by civilians or the Armed Forces of Ukraine, the Ministry of Internal Affairs, the Border Guard, etc.
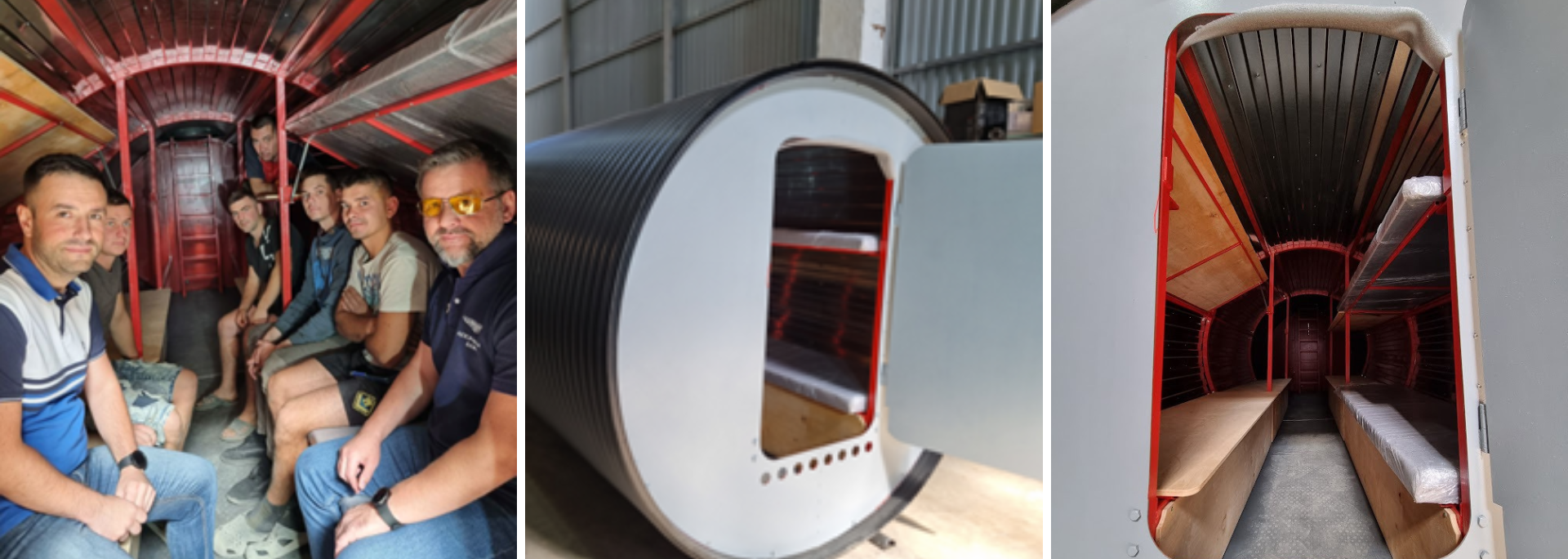
(An underground shelter from Pipes.One)
The company also considers playing a role in the reconstruction of Ukraine. For instance, a mobile pipe production unit can help to quickly rebuild pipeline infrastructure such as sewerage, drainage and irrigation systems. This type of work is required in the Kherson region, which happens to be the home region of some of the company’s employees. This agricultural region, the largest arable land area in Ukraine, has been heavily devastated due to Russian armed aggression. Innovations like the one from Ukrainian Pipes.One can help revive agriculture in the area.

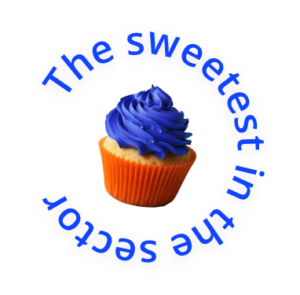
ABOUT THE PROJECT
«The Cream of the Crop of Ukrainian Cleantech» is a series of stories about 10 Ukrainian companies that received the Climate Innovation Vouchers grant at a key stage of their development. They've risen to prominence in Ukraine's cleantech sector in a short span. Climate Innovation Vouchers is one of the largest grant programs in Ukraine for innovators in green and climate-friendly technologies. It was initiated by the European Bank for Reconstruction and Development and funded by the European Union. NGO Greencubator implements the program in Ukraine.