Ukrainian company “Chervona Hvilya” brings cleantech to aircraft titan details manufacturing
Green Bottom-Line
Industrial companies all over the world are trying hard to cut their resource usage, and be more energy-efficient. Yet they remain the largest environment pollutants, producing millions of tons of CO2 emissions and churning out millions tons of industrial waste every year.
Though, for these companies producing tangible products environment is by far not the biggest concern. Using less natural resources and less energy is not only good for environment, but for many companies bottom-lines as well. Especially with governments in developed countries which intensify the taxation of those producers who pollute heavily.
Aerospace engineering is clearly among the leaders of those industries truly eager and dedicated to resource-saving. Mainly because modern aircraft production just needs lots of raw materials, each of them having its own heavy CO2 footprint and hefty price tag. Titanium is among these expensive but crucially important materials for plane-makers. The bad news for aircraft industry is that more than 50% of it is just wasted. Most of it becomes scraps after CNC machines carve out complex shapes of aircraft details out of titanium pieces.
The good news though his provides a fertile soil for technologies which can save on using titanium and Ukrainian company “Chervona Hvilya” did just that with their titanium 3D printing technology. With material savings reaching up to 90%, it is no wonder that aircraft producers were the first to become their customers.
Printing the Savings
3D printing, as a technology that aims to use less materials, and therefore reduce CO2 emissions, has already proved it’s climate friendliness being widely spread in consumer industry. Less materials to make a unit or detail means less energy used. Moreover, these savings are getting multiplied throughout the whole production chain: less materials means less of ore mined, less electricity and fuel used to transport and process it.
Recently Ukrainian company “Chervona Hvilya” presented an adaptation of 3D printing to the metal manufacturing industry as well as solid details manufacture. Innovators managed to develop and put into operation their own device. One that can print details with the ultra stable titanium.
The experimental device for metal 3D printing looks rather ordinary than innovative, neither photos no video can give a sense of the cutting-edge tech densely packed inside. One can not tell why the technology is greener than others by just looking at it. Though, numbers tell a compelling story about titanium 3D printing contribution into reducing climate impact and resource usage.
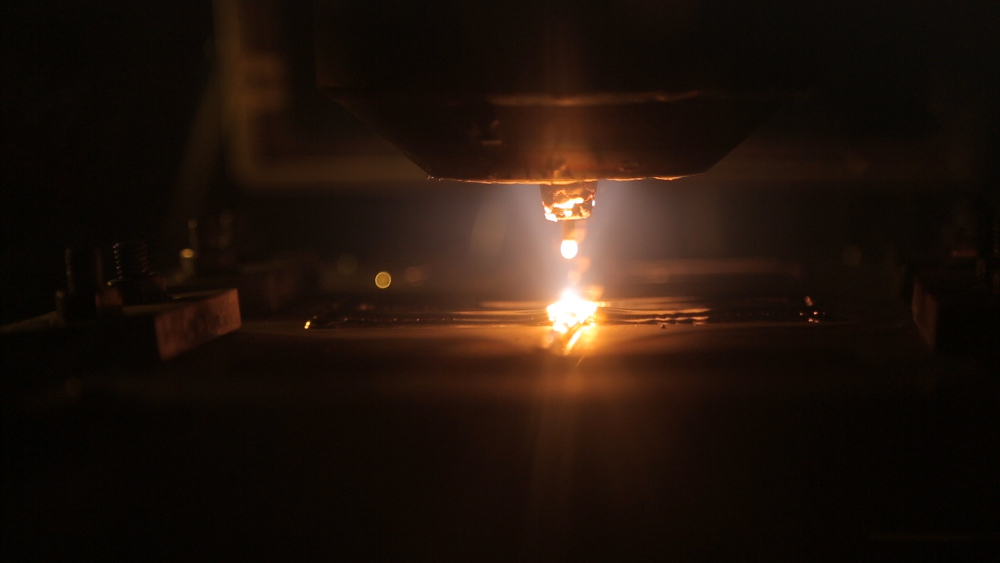
Titanium 3D printing
1 kg of titanium production results in about 35 kg of CO2 emissions, and we need 20-30 kg of titanium to produce a detail X with a traditional manufacture method. But with xBeam 3D Metal Printing technology that very same detail can be mastered with only 3-5 kg of titanium. Considering this, 3D printing should become an environmental duty of the aviation industry, and the most progressive companies are already working to integrate “Chervona Hvilya” product into manufacture processes.
The company recently won a grant under the Climate Innovation Vouchers Program which they plan to use for integrating best industrial CAD / CAM software into their product and completing their solution as a full-cycle industrial 3D printing system. Dmytro Kovalchuk, CEO, “Chervona Hvilya”, shared his experience of renovating the world’s steel industry and making it greener.
From traditional metallurgy to 3D printing
— Our company has been engaged in high-tech processes for over 20 years: titanium production, ingot production, etc. Ukraine is among world’s leaders in electron-beam technologies and other high-tech metallurgical processes. Ukraine has always had a well-organized titanium industry. Some time ago our company has noticed the growth of global demand for new tech solutions in metal manufacture. That is why we decided to switch from making titanium products to develop devices for titanium products manufacturing.
In 2005, we started designing and putting together special equipment based on the electronic gas-filled gun, developed together with our colleagues from the Kyiv Polytechnic Institute. We delivered our equipment all around the world, introduced our technology, shared experience with foreign specialists and discovered popular market trends.
Analyzing all that information we found out that global metallurgy, particularly the one that deals with expensive materials, seeks for resource and energy saving, as well as moves toward manufacturing processes acceleration. To meet all these demands we’ve ended up in 3D printing. We’ve developed our own technology, based on the outstanding characteristics of our electron-beam gun (you can not find on the market any comparable equipment), patented it, and then designed a pilot system called xBeam 3D Metal Printing. This experimental 3D printer can print with a metal wire a wide range of products using various materials.
We were able to create the first experimental 3D printing setup soon enough, because at that time all the members of our team have already had solid background. The guys from Kyiv Polytechnic Institute added their huge intellectual investment as the developers of our electron-beam gun. So, on the one hand, we got complete device just in two years. On the other hand, it is fair enough to note that the process was so quick due to 20-30-40 years of experience of the involved professionals.
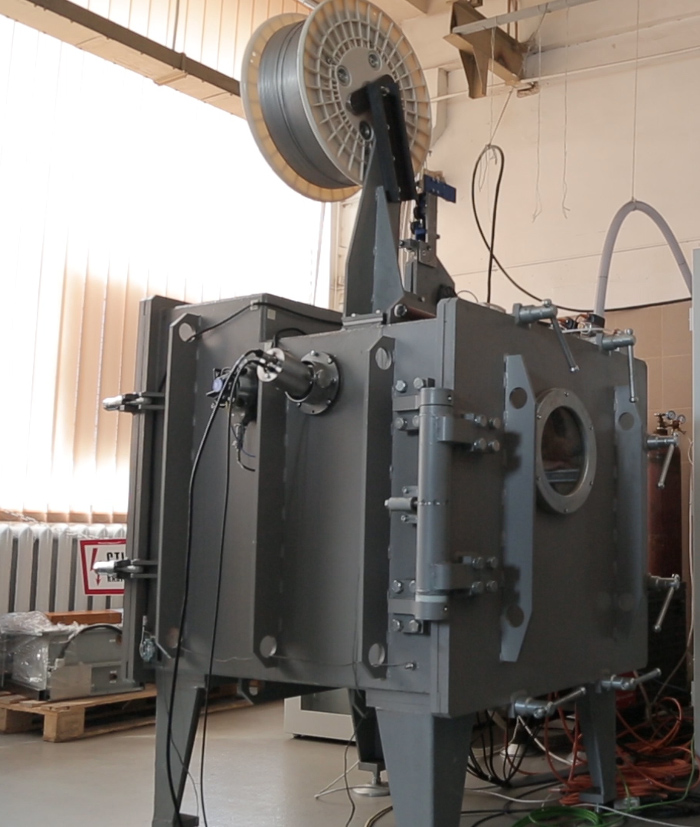
Cleantech doesn’t have to look extraordinary
Technology Explained
— 3D printing is an automatic process, and for us it is a new approach, compared to a traditional metallurgical technology. Therefore now we develop and test new software solutions for 3D printing automatic process, as well as for monitoring and quality control systems.
As aerospace industry is the main driver for the steel 3D printing development in the world, it sets high quality and safety standards for products, and we have to meet these requirements. Last year we’ve made agreements with leading international companies to research the properties of materials produced with our technology. Independent research centers carried out necessary research. The results confirmed significant advantages of the materials and details that we provide with our own production technology.
As for productivity, we reached 3 kg of printed details per hour, because material consumption is the main characteristic of such printing, not the quantity of details (they may be of different shapes, weight and size). During the three-shift schedule 3D printing device can print 35-40 kg of details per day. Which is, in monetary terms, gives us the potential market value of printing no more than $ 250-300 / kg of printed product.
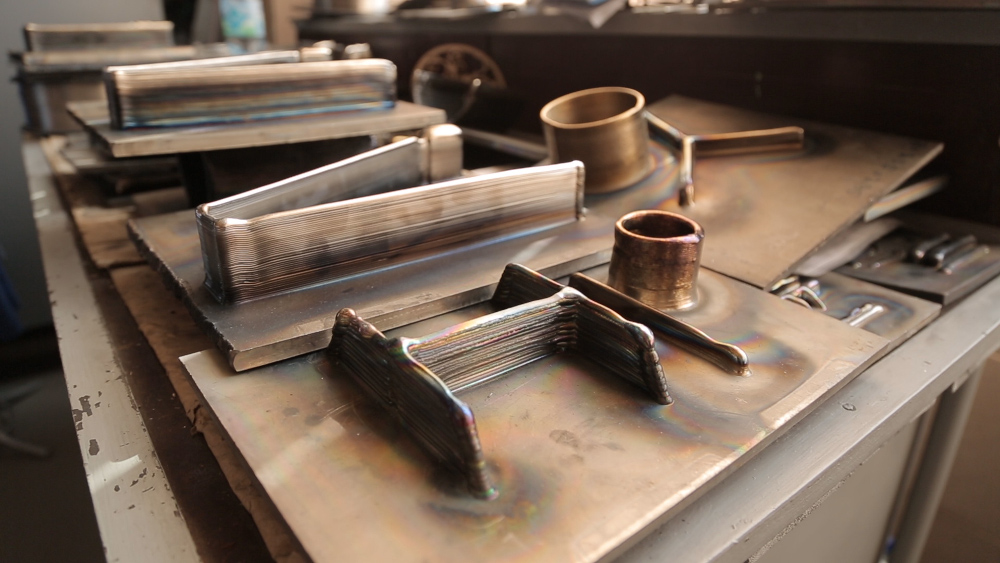
Produced by xBeam 3D Metal Printing
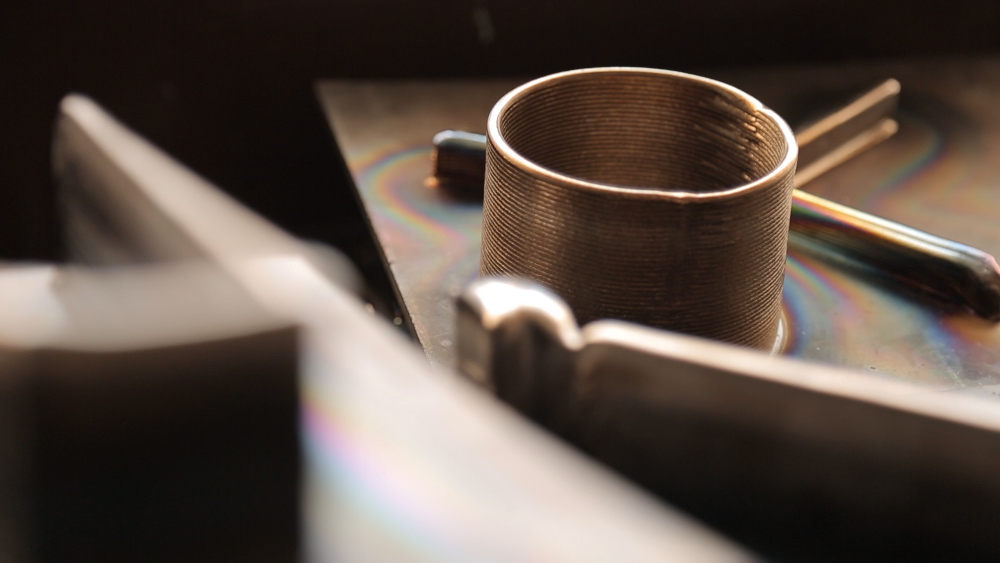
Produced by xBeam 3D Metal Printing
Accelerated by Climate Vouchers
— To enter this titanium 3D printing market we needed to implement many new technical and software solutions, process automation, that is different from the systems that we created before. As a private company we search for additional funding, so we considered the Climate Innovation Voucher program as an opportunity to accelerate our 3D printing project.
The green cleantech component is in the very essence of the 3D printing technology. Actually, metal 3D printing itself was created to save the resources. Using less raw materials to create new details, this technology helps to save energy for extraction and processing of work stock. With 1 kg titanium production, 35 kg of CO2 emissions are generated, and 3D printing reduces the use of titanium for the production of different details. This technique gives an opportunity to use 2-3 kg of titanium to manufacture 1 kg weight detail, instead of 10-20 kg of material used for the same detail before. And this is not only about saving titanium, but also about the reduction of harmful emissions into the atmosphere.
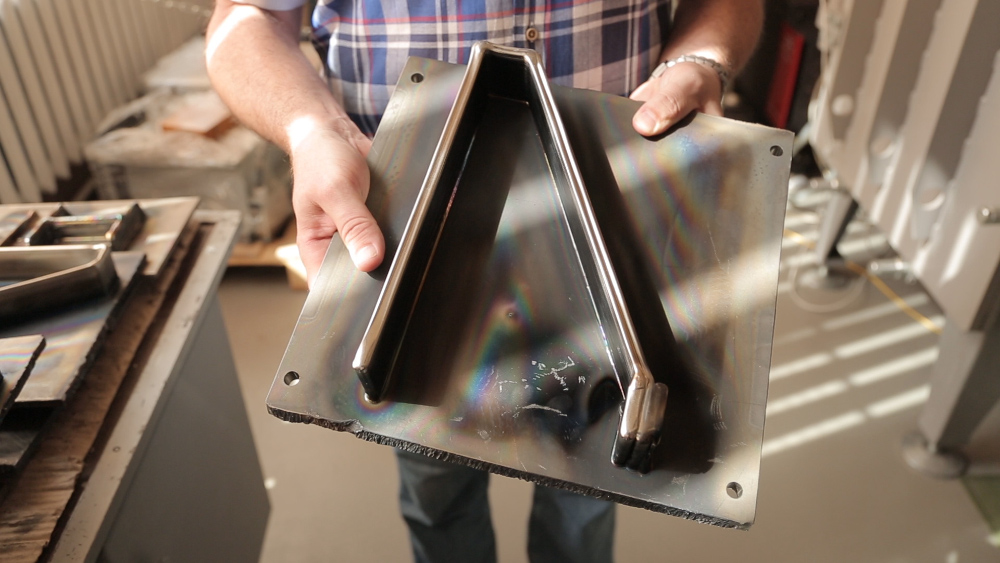
One of those details, made with titanium saving 3D printing
Due to our green contribution to the industry our company received a grant under the Climate Innovation Voucher program. We do already cooperate with the company AMS International, also with the Ukrainian company “Photon-Service”, whose experts create and adapt software to customize our technological process.
Meeting tough aerospace requirements
— The aerospace industry is the main driver of the metallic 3D printing technology, since resource conservation is always relevant for expensive materials. Titanium, as well as nickel, and so on are used widely in this sphere. Airbus, Boeing, NASA, Lockheed Martin Corporation are pioneers in financing such new projects, also implementing it into production after all proper tests. In 2017, the first titanium detail printed on a 3D wire printer was installed on a Boeing-787 civilian aircraft. This is a very good precedent and a very good signal for developers, as well as for the whole potential market for such equipment.
That detail isn’t ours yet, but we are moving the same way. Now we are producing test examples for our foreign customers. They will be able to check not only the quality of the metal we create, but also the whole range of other product requirements. These include geometric dimensions, economic feasibility, accuracy, quality of whole details rather than individual fragments and real manufacturing test methods.
This year we hope to get feedback from our customers on the test details already completed to improve prototypes of industrial systems, basing on their feedback. With the new software, which we are developing right now thanks to the Climate Vouchers, we are on the final stage of industrial system creation already.
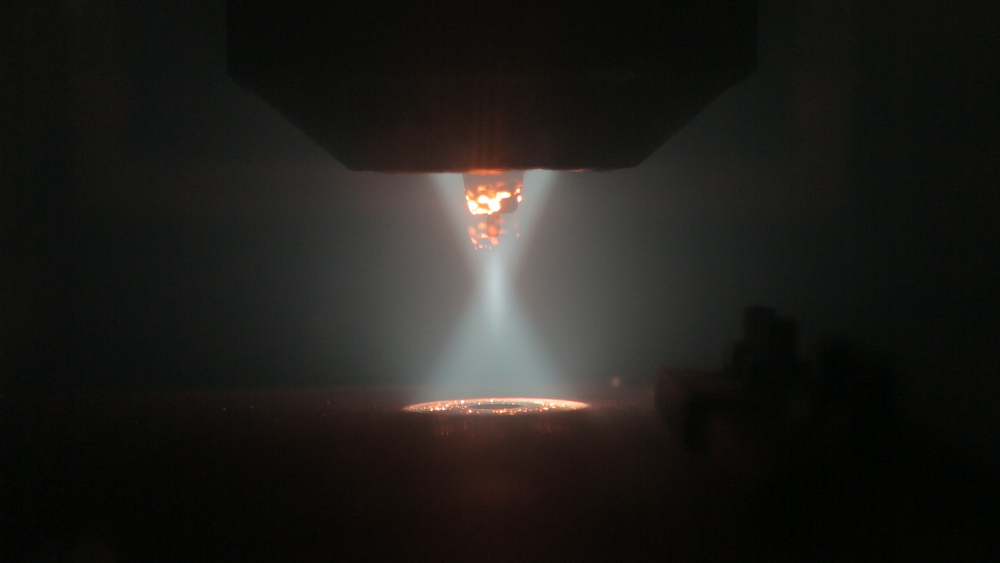
Getting ready to start titanium print
Ahead to Ukrainian market
— I mentioned foreign partners, but Ukrainian aerospace industry is also interested in our project. CB Antonova, CB “Yuzhnoye”, and Motor Sich — we have arrangements to manufacture test details with all of them. All our testing is free of charge for Ukrainian companies, because we want to implement the results of our work in Ukraine as quickly as possible.
I would like to add that since there are not many financial sources available for private business in Ukraine, we do really appreciate the opportunities provided by Climate Innovation Voucher. It’s great to have such programs in our country, but it is also important to inform the widest range of developers about these financial tools: both from private business and from government enterprises, from research organizations and small companies. Therefore, the work of Greencubator, as a coordinator of this program and other climate projects in Ukraine, is hard to overestimate. Green projects support is an example of synergy when all parties do benefit. We are working on preserving resources which is equally important for all the inhabitants of the Earth.
A tangible saving of the material, moreover, with the green component, is the solution that industry needs today. It is the importance of titanium 3D printing as a climate technology that contributed to receiving a grant under the Climate Innovation Vouchers program by “Chervona Hvilya”. The Program is implemented by the NGO Greencubator, launched as a part of the EBRD program “Finance and Technology Transfer Centre for Climate Change” (FINTECC), funded by the European Union. Read about other winners of the project on the website of Climate Innovations Vouchers.